El equipo de José Manuel Serra (a la derecha). Fuente: UPV.
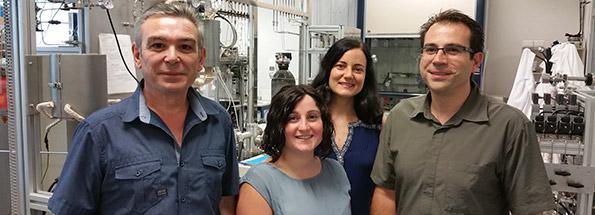
Una novedosa investigación internacional liderada por el Instituto de Tecnología Química (ITQ), centro mixto de la Universitat Politècnica de València (UPV) y el Consejo Superior de Investigaciones Científicas (CSIC), abre la puerta al uso generalizado del gas natural no sólo como mero combustible de calefacción, sino como fuente de productos químicos y nuevos combustibles de automoción.
El trabajo, cuyos resultados han sido publicados por la revista Science, podría resolver las actuales dificultades para hacer rentable económicamente, en muchos casos, la explotación del gas natural como fuente de hidrocarburos.
Jose Manuel Serra, profesor del CSIC y director del estudio, explica en la nota de prensa de la UPV que el equipo ha desarrollado "una nueva arquitectura de reactor catalítico que permite la transformación directa del metano en hidrocarburos líquidos más fácilmente transportables y de mayor valor añadido".
"El metano es el componente mayoritario en el gas natural y en el biogás de fermentaciones naturales, mientras que el producto principal de nuestro proceso es benceno", añade.
Además, el trabajo desarrollado por los investigadores del ITQ presenta también importantes ventajas medioambientales. "Se trata de una transformación más limpia, ya que al ser un proceso directo y con alto rendimiento, las emisiones de dióxido de carbono son mínimas", destaca Serra.
Junto a los investigadores del ITQ, han participado en este proyecto la Universidad de Oslo (Noruega) y la empresa multinacional norteamericana CoorsTek, de cerámicas avanzadas.
Cambio en las 'reglas del juego'
El benceno es el producto de partida en la industria química para infinidad de productos cotidianos, tales como todo tipo de plásticos, tejidos, adhesivos, pinturas, jabones, combustible de aviación, etc. Ahora, este producto se obtiene del petróleo. Sin embargo, la nueva ruta ideada por los investigadores del ITQ a partir del gas natural podría cambiar las reglas de juego en este sector industrial con enorme peso en la economía global.
Hasta el momento, esta reacción se llevaba a cabo de manera selectiva sobre catalizadores (zeolitas), y su industrialización se veía frenada por dos problemas.
En primer lugar, el catalizador perdía rápidamente actividad debido a la formación de carbón, que bloqueaba el reactor. En segundo, el rendimiento de esta reacción está limitado por el equilibrio químico natural y este límite no se puede sobrepasar por los medios convencionales utilizados por los químicos e ingenieros químicos (como variar la presión o temperatura).
El trabajo, cuyos resultados han sido publicados por la revista Science, podría resolver las actuales dificultades para hacer rentable económicamente, en muchos casos, la explotación del gas natural como fuente de hidrocarburos.
Jose Manuel Serra, profesor del CSIC y director del estudio, explica en la nota de prensa de la UPV que el equipo ha desarrollado "una nueva arquitectura de reactor catalítico que permite la transformación directa del metano en hidrocarburos líquidos más fácilmente transportables y de mayor valor añadido".
"El metano es el componente mayoritario en el gas natural y en el biogás de fermentaciones naturales, mientras que el producto principal de nuestro proceso es benceno", añade.
Además, el trabajo desarrollado por los investigadores del ITQ presenta también importantes ventajas medioambientales. "Se trata de una transformación más limpia, ya que al ser un proceso directo y con alto rendimiento, las emisiones de dióxido de carbono son mínimas", destaca Serra.
Junto a los investigadores del ITQ, han participado en este proyecto la Universidad de Oslo (Noruega) y la empresa multinacional norteamericana CoorsTek, de cerámicas avanzadas.
Cambio en las 'reglas del juego'
El benceno es el producto de partida en la industria química para infinidad de productos cotidianos, tales como todo tipo de plásticos, tejidos, adhesivos, pinturas, jabones, combustible de aviación, etc. Ahora, este producto se obtiene del petróleo. Sin embargo, la nueva ruta ideada por los investigadores del ITQ a partir del gas natural podría cambiar las reglas de juego en este sector industrial con enorme peso en la economía global.
Hasta el momento, esta reacción se llevaba a cabo de manera selectiva sobre catalizadores (zeolitas), y su industrialización se veía frenada por dos problemas.
En primer lugar, el catalizador perdía rápidamente actividad debido a la formación de carbón, que bloqueaba el reactor. En segundo, el rendimiento de esta reacción está limitado por el equilibrio químico natural y este límite no se puede sobrepasar por los medios convencionales utilizados por los químicos e ingenieros químicos (como variar la presión o temperatura).
Separación selectiva de hidrógeno
"La clave de nuestro proceso", indica el profesor Serra, "es el uso de una membrana que separa selectivamente hidrógeno e inyecta oxígeno durante la reacción de transformación del metano, y se lleva a cabo mediante la aplicación digitalizada de corriente eléctrica.
De este modo, es posible sobrepasar el equilibrio termodinámico y conseguir rendimientos más elevados y estables en el tiempo. Como consecuencia de ello, como subproducto directo de este reactor se obtiene una gran cantidad de hidrógeno de alta pureza, que es un combustible totalmente limpio con elevada densidad energética".
"A nivel macro", añade, "es realmente muy simple: gas abundante y barato transformado en un líquido valioso a través de un proceso limpio y barato. A nivel nanoquímico, sin embargo, ahí donde las moléculas interactúan con catalizador y membrana a una temperatura de alrededor de 700 ° C, había muchos factores que diseñar y controlar para obtener sólo las moléculas necesarias para que el nuevo proceso funcionara".
Otros aspectos de especial relevancia para la industria son tanto el pequeño tamaño de los convertidores directos de gas natural como su modularidad, lo que permite adaptar el tamaño de la planta al del yacimiento o fuente de gas natural.
Ello supone una gran ventaja frente a los procesos industriales actuales, basados en múltiples etapas consecutivas y que requieren de tamaños de planta gigantescos (e inversiones proporcionales) para su rentabilidad.
Las membranas de cerámica, informa la empresa Coorstek en una nota de prensa, están hechas de materiales abundantes como bario y zirconio, que se encuentran en los depósitos de arena de gran tamaño, con la adición de capas electro-catalíticas delgadas de metales abundantes como el níquel y el cobre.
"Con una fabricación de alto volumen, podemos hacer reactores de membrana de cerámica activos que son competitivos en costes con los reactores catalíticos convencionales de procesamiento de gas", dice Per Vestre, director general de Ciencias de Membrana de Coorstek. "Si bien los costes de los reactores serán similares, los resultados que habilita este nuevo proceso tienen el potencial de mejorar significativamente tanto los costes financieros como ambientales de la producción de sustancias químicas."
La Universidad Politécnica de Valencia pertenece al ecosistema de innovación Global Imast, que pertenece al grupo eGauss, y que celebrará su evento anual el 23 de noviembre en varias sedes de toda España.
"La clave de nuestro proceso", indica el profesor Serra, "es el uso de una membrana que separa selectivamente hidrógeno e inyecta oxígeno durante la reacción de transformación del metano, y se lleva a cabo mediante la aplicación digitalizada de corriente eléctrica.
De este modo, es posible sobrepasar el equilibrio termodinámico y conseguir rendimientos más elevados y estables en el tiempo. Como consecuencia de ello, como subproducto directo de este reactor se obtiene una gran cantidad de hidrógeno de alta pureza, que es un combustible totalmente limpio con elevada densidad energética".
"A nivel macro", añade, "es realmente muy simple: gas abundante y barato transformado en un líquido valioso a través de un proceso limpio y barato. A nivel nanoquímico, sin embargo, ahí donde las moléculas interactúan con catalizador y membrana a una temperatura de alrededor de 700 ° C, había muchos factores que diseñar y controlar para obtener sólo las moléculas necesarias para que el nuevo proceso funcionara".
Otros aspectos de especial relevancia para la industria son tanto el pequeño tamaño de los convertidores directos de gas natural como su modularidad, lo que permite adaptar el tamaño de la planta al del yacimiento o fuente de gas natural.
Ello supone una gran ventaja frente a los procesos industriales actuales, basados en múltiples etapas consecutivas y que requieren de tamaños de planta gigantescos (e inversiones proporcionales) para su rentabilidad.
Las membranas de cerámica, informa la empresa Coorstek en una nota de prensa, están hechas de materiales abundantes como bario y zirconio, que se encuentran en los depósitos de arena de gran tamaño, con la adición de capas electro-catalíticas delgadas de metales abundantes como el níquel y el cobre.
"Con una fabricación de alto volumen, podemos hacer reactores de membrana de cerámica activos que son competitivos en costes con los reactores catalíticos convencionales de procesamiento de gas", dice Per Vestre, director general de Ciencias de Membrana de Coorstek. "Si bien los costes de los reactores serán similares, los resultados que habilita este nuevo proceso tienen el potencial de mejorar significativamente tanto los costes financieros como ambientales de la producción de sustancias químicas."
La Universidad Politécnica de Valencia pertenece al ecosistema de innovación Global Imast, que pertenece al grupo eGauss, y que celebrará su evento anual el 23 de noviembre en varias sedes de toda España.
Referencia bibliográfica:
S. H. Morejudo, R. Zanón, S. Escolástico, I. Yuste-Tirados, H. Malerød-Fjeld, P. K. Vestre, W. G. Coors, A. Martínez, T. Norby, J. M. Serra, C. Kjølseth: Direct conversion of methane to aromatics in a catalytic co-ionic membrane reactor. Science (2016). DOI: 10.1126/science.aag0274.
S. H. Morejudo, R. Zanón, S. Escolástico, I. Yuste-Tirados, H. Malerød-Fjeld, P. K. Vestre, W. G. Coors, A. Martínez, T. Norby, J. M. Serra, C. Kjølseth: Direct conversion of methane to aromatics in a catalytic co-ionic membrane reactor. Science (2016). DOI: 10.1126/science.aag0274.