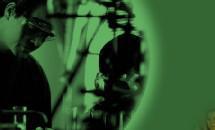
Ingenieros del departamento de ingeniería química y ciencia de los materiales de la Universidad de Minessota, liderados por el investigador Lanny D. Schmidt, han ideado un proceso que permite producir combustibles y productos químicos completamente renovables a partir del calentamiento rápido del aceite vegetal o del azúcar, dando lugar a monóxido de carbono e hidrógeno.
Cuando calentamos azúcar o aceite vegetal, el azúcar se pone negra y el aceite suelta mucho humo y acaba poniéndose de color marrón oscuro. Estas reacciones se originan por la descomposición de ambos productos hasta formar carbón.
Si el aceite y el azúcar son calentados un millón de veces más deprisa de lo que lo haríamos en una cocina, sin embargo, el producto es diferente: una mezcla gaseosa denominada gas de síntesis (formado por hidrógeno y CO, CO + H2) que puede utilizarse para sintetizar combustibles y productos químicos y obtener gasolina sintética.
La gasolina sintética, creada durante la segunda guerra mundial por la industria química alemana, se utiliza principalmente en la actualidad como un aditivo del diesel. Sin embargo, están en marcha diferentes líneas de investigación, especialmente unidades GTL (Gas to liquid), con la finalidad de ampliar sus aplicaciones y de limitar sus efectos contaminantes, pero hasta el momento las perspectivas de su implantación son limitadas debido a su elevado costo. El procedimiento ideado por los ingenieros norteamericanos puede provocar cambios en esta situación.
Proceso más rápido
El gas de síntesis puede obtenerse a partir de la biomasa, pero el gran obstáculo del uso de biomasa como fuente de energía es la ausencia de un proceso lo suficientemente rápido y barato capaz de convertirla en un combustible utilizable.
La biomasa es la materia orgánica originada en un proceso biológico y que puede utilizarse para la obtención de la llamada bioenergía. La biomasa se utiliza para generación de calor, frío, electricidad o transporte. Para facilitar su uso se transforma en biocombustible sólido, líquido (como biodiésel o bioetanol) o gaseoso, como el biogás.
El proceso actual que convierte la biomasa en una mezcla de hidrogeno (H2) y monóxido de carbono (CO), llamado gasificación, es relativamente lento, y requiere de procesos largos y complejos, así como de un equipamiento caro que debe instalarse en lugares concretos
Sin embargo, el proceso descubierto por Schmidt y sus colaboradores convierte rápidamente los líquidos en hidrógeno y CO, mediante un reactor químico muy simple que usa un catalizador para acelerar la reacción. De este proceso no se genera carbón, sino la mezcla de gases. Los investigadores han demostrado sus posibilidades con dos alimentos comunes: el aceite vegetal y el agua azucarada.
En qué consiste
Según explican en la revista Science, el sistema consiste en que las gotas de combustibles no volátiles, como el aceite de soja o las de las soluciones de glucosa y agua, sean rápidamente evaporadas por una oxidación catalítica parcial para producir hidrógeno con un alto rendimiento y en un tiempo récord: menos de 50 milisegundos.
La pirólisis (o descomposición química de materia orgánica causada por el calentamiento en ausencia de oxígeno u otros reactivos), unida con la oxidación catalítica de los compuestos y sus fragmentos tras el impacto con una superficie catalítica caliente y de los materiales rodio-cerio, impide la formación de capas de carbón sobre el catalizador. La reacción catalítica de estos productos genera aproximadamente un megavatio de calor por metro cuadrado, lo que mantendría la superficie catalítica a 800 ºC.
A estas temperaturas, los combustibles pueden transformarse directamente en hidrógeno y monóxido de carbono, así como en otras pequeñas moléculas sin que se forme el carbón. Así, este nuevo proceso descompone las moléculas largas convirtiéndolas en moléculas más pequeñas, que pueden reaccionar para formar el gas de síntesis en lugar de quemarse y formar carbón.
Esto se ha logrado utilizando un inyector de combustible automotor que rocía pequeñas gotas de líquido directamente sobre una superficie cerámica porosa y encendida. Al impactar con dicha superficie, estas gotas se descomponen en diminutos elementos que reaccionan con el aire en la superficie del catalizador. La reacción con el aire hace que el proceso se desarrolle a una temperatura muy alta sin necesidad de una fuente de calor, lo que permite simplificar el sistema.
Retos en el desarrollo
Algunos de los retos más significativos para que el proceso funcione han sido el desarrollo de un procedimiento de encendido efectivo que suprima las llamas y el diseño de un sistema reactivo capaz de liberar combustible y oxígeno al catalizador para que el proceso opere de manera estable y autotérmica.
El sistema, aún siendo pequeño y simple, potencialmente puede ampliarse y aplicarse a mayor escala. La novedad es que permite que pequeñas gotas de líquido impacten en una superficie muy caliente y se conviertan en gases sin dar lugar a la formación de carbón.
Esto se consigue gracias a que las gotas no llegan a enfriar la superficie debido a que está recubierta con el catalizador (rodio-cerio) y, gracias a la presencia del oxígeno, los fragmentos derivados de la descomposición del aceite reaccionan con él en la superficie catalítica para formar hidrógeno y CO y generar el calor necesario para mantener la superficie caliente.
Los pasos de este proceso son extremadamente rápidos y complejos: las gotas impactan la superficie a gran velocidad, se rompen y se transforman en gotas más pequeñas. La formación de la capa de vapor reactivo entre la gota y la superficie, y la penetración de los fragmentos en los poros de la capa catalítica, suceden en milésimas de segundo, según explica la revista Scitizen, que comenta el descubrimiento.
Posibles aplicaciones
Gracias a la rapidez del proceso, potencialmente podrían derivarse varias tecnologías a partir de él. El hecho de que no se necesite calor externo para mantener la superficie del catalizador lo suficientemente caliente para una reacción continua, permite que dicho catalizador se utilice para acelerar procesos que no forman carbón.
Asimismo, este catalizador puede especificar ciertas reacciones para otros productos como el olefino, que serviría para la producción de polímeros a partir de fuentes renovables.
El sistema podría ser aplicado incluso a mayor escala, pero aún queda por definir el papel de las impurezas y si la estabilidad podría mantenerse a largo plazo. La tecnología tendría aplicaciones en el uso de la biomasa para la generación de hidrógeno y células combustibles y, tal vez, la generación de gas de síntesis para la producción de combustibles líquidos.
Cuando calentamos azúcar o aceite vegetal, el azúcar se pone negra y el aceite suelta mucho humo y acaba poniéndose de color marrón oscuro. Estas reacciones se originan por la descomposición de ambos productos hasta formar carbón.
Si el aceite y el azúcar son calentados un millón de veces más deprisa de lo que lo haríamos en una cocina, sin embargo, el producto es diferente: una mezcla gaseosa denominada gas de síntesis (formado por hidrógeno y CO, CO + H2) que puede utilizarse para sintetizar combustibles y productos químicos y obtener gasolina sintética.
La gasolina sintética, creada durante la segunda guerra mundial por la industria química alemana, se utiliza principalmente en la actualidad como un aditivo del diesel. Sin embargo, están en marcha diferentes líneas de investigación, especialmente unidades GTL (Gas to liquid), con la finalidad de ampliar sus aplicaciones y de limitar sus efectos contaminantes, pero hasta el momento las perspectivas de su implantación son limitadas debido a su elevado costo. El procedimiento ideado por los ingenieros norteamericanos puede provocar cambios en esta situación.
Proceso más rápido
El gas de síntesis puede obtenerse a partir de la biomasa, pero el gran obstáculo del uso de biomasa como fuente de energía es la ausencia de un proceso lo suficientemente rápido y barato capaz de convertirla en un combustible utilizable.
La biomasa es la materia orgánica originada en un proceso biológico y que puede utilizarse para la obtención de la llamada bioenergía. La biomasa se utiliza para generación de calor, frío, electricidad o transporte. Para facilitar su uso se transforma en biocombustible sólido, líquido (como biodiésel o bioetanol) o gaseoso, como el biogás.
El proceso actual que convierte la biomasa en una mezcla de hidrogeno (H2) y monóxido de carbono (CO), llamado gasificación, es relativamente lento, y requiere de procesos largos y complejos, así como de un equipamiento caro que debe instalarse en lugares concretos
Sin embargo, el proceso descubierto por Schmidt y sus colaboradores convierte rápidamente los líquidos en hidrógeno y CO, mediante un reactor químico muy simple que usa un catalizador para acelerar la reacción. De este proceso no se genera carbón, sino la mezcla de gases. Los investigadores han demostrado sus posibilidades con dos alimentos comunes: el aceite vegetal y el agua azucarada.
En qué consiste
Según explican en la revista Science, el sistema consiste en que las gotas de combustibles no volátiles, como el aceite de soja o las de las soluciones de glucosa y agua, sean rápidamente evaporadas por una oxidación catalítica parcial para producir hidrógeno con un alto rendimiento y en un tiempo récord: menos de 50 milisegundos.
La pirólisis (o descomposición química de materia orgánica causada por el calentamiento en ausencia de oxígeno u otros reactivos), unida con la oxidación catalítica de los compuestos y sus fragmentos tras el impacto con una superficie catalítica caliente y de los materiales rodio-cerio, impide la formación de capas de carbón sobre el catalizador. La reacción catalítica de estos productos genera aproximadamente un megavatio de calor por metro cuadrado, lo que mantendría la superficie catalítica a 800 ºC.
A estas temperaturas, los combustibles pueden transformarse directamente en hidrógeno y monóxido de carbono, así como en otras pequeñas moléculas sin que se forme el carbón. Así, este nuevo proceso descompone las moléculas largas convirtiéndolas en moléculas más pequeñas, que pueden reaccionar para formar el gas de síntesis en lugar de quemarse y formar carbón.
Esto se ha logrado utilizando un inyector de combustible automotor que rocía pequeñas gotas de líquido directamente sobre una superficie cerámica porosa y encendida. Al impactar con dicha superficie, estas gotas se descomponen en diminutos elementos que reaccionan con el aire en la superficie del catalizador. La reacción con el aire hace que el proceso se desarrolle a una temperatura muy alta sin necesidad de una fuente de calor, lo que permite simplificar el sistema.
Retos en el desarrollo
Algunos de los retos más significativos para que el proceso funcione han sido el desarrollo de un procedimiento de encendido efectivo que suprima las llamas y el diseño de un sistema reactivo capaz de liberar combustible y oxígeno al catalizador para que el proceso opere de manera estable y autotérmica.
El sistema, aún siendo pequeño y simple, potencialmente puede ampliarse y aplicarse a mayor escala. La novedad es que permite que pequeñas gotas de líquido impacten en una superficie muy caliente y se conviertan en gases sin dar lugar a la formación de carbón.
Esto se consigue gracias a que las gotas no llegan a enfriar la superficie debido a que está recubierta con el catalizador (rodio-cerio) y, gracias a la presencia del oxígeno, los fragmentos derivados de la descomposición del aceite reaccionan con él en la superficie catalítica para formar hidrógeno y CO y generar el calor necesario para mantener la superficie caliente.
Los pasos de este proceso son extremadamente rápidos y complejos: las gotas impactan la superficie a gran velocidad, se rompen y se transforman en gotas más pequeñas. La formación de la capa de vapor reactivo entre la gota y la superficie, y la penetración de los fragmentos en los poros de la capa catalítica, suceden en milésimas de segundo, según explica la revista Scitizen, que comenta el descubrimiento.
Posibles aplicaciones
Gracias a la rapidez del proceso, potencialmente podrían derivarse varias tecnologías a partir de él. El hecho de que no se necesite calor externo para mantener la superficie del catalizador lo suficientemente caliente para una reacción continua, permite que dicho catalizador se utilice para acelerar procesos que no forman carbón.
Asimismo, este catalizador puede especificar ciertas reacciones para otros productos como el olefino, que serviría para la producción de polímeros a partir de fuentes renovables.
El sistema podría ser aplicado incluso a mayor escala, pero aún queda por definir el papel de las impurezas y si la estabilidad podría mantenerse a largo plazo. La tecnología tendría aplicaciones en el uso de la biomasa para la generación de hidrógeno y células combustibles y, tal vez, la generación de gas de síntesis para la producción de combustibles líquidos.