Micrografía electrónica de transmisión del nanocompuesto (poli éter imida-poli butiléntereftalato)/nanotubos de carbono con 3% de nanotubos. Fuente: UPV-EHU.
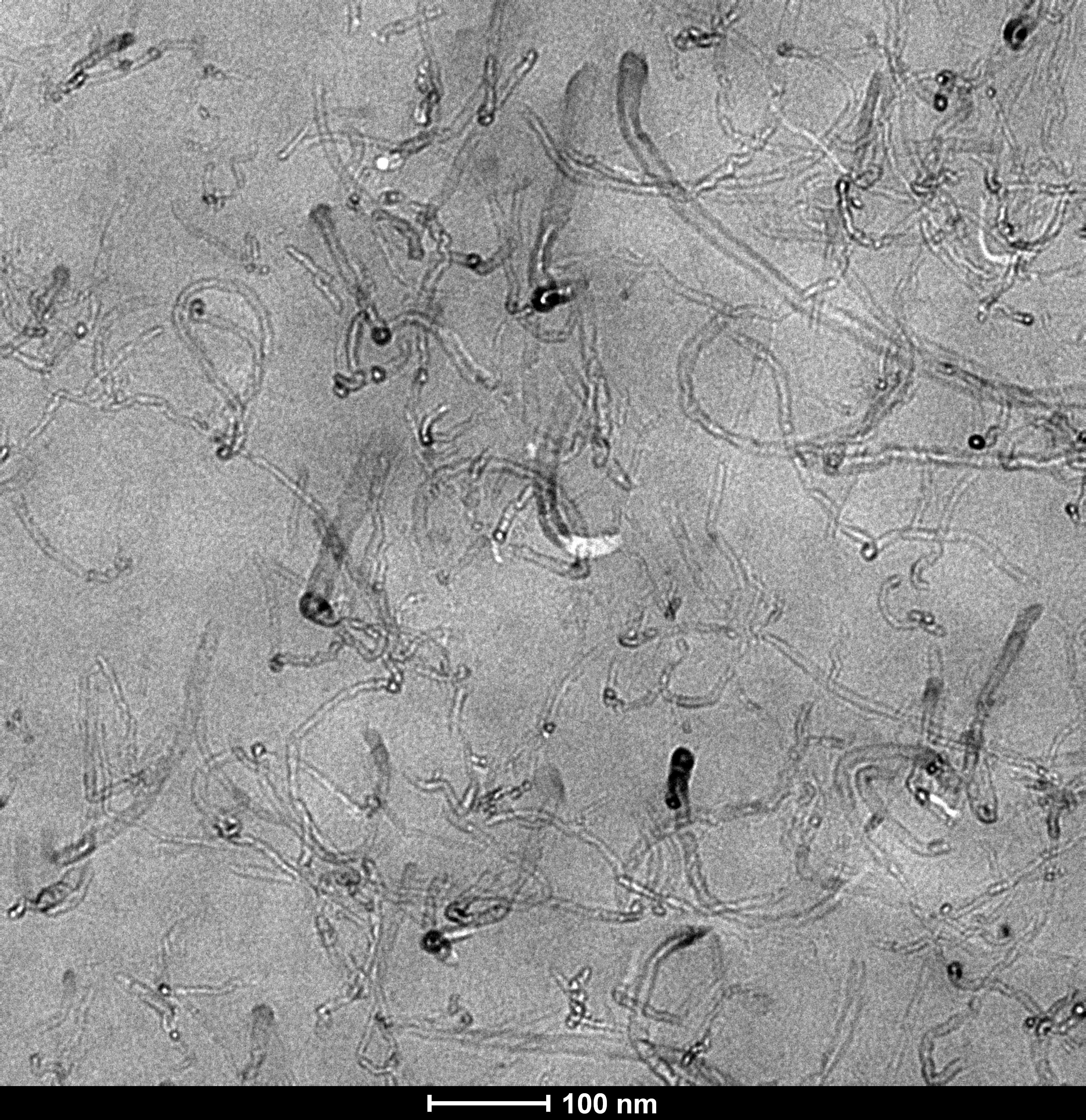
Un estudio de la Universidad del País Vasco/EHU ha obtenido magníficos resultados en la mejora de las propiedades mecánicas y de conductividad eléctrica del polímero poli éter imida (PEI), empleado entre otras cosas para desarrollar piezas de los aviones, gracias al empleo de nanotubos de carbono.
Los nanotubos de carbono tienen unas propiedades mecánicas excelentes, son muy resistentes, muy rígidos, y además, son conductores de la electricidad. "El problema que tienen es que se dispersan, es decir, se mezclan con mucha dificultad con los polímeros" señala Iñaki Eguiazabal, miembro del Grupo de Tecnología de Polímeros, en la nota de prensa de la UPV.
Por ello, es fundamental encontrar métodos que permitan alcanzar un alto grado de dispersión y de estabilidad de los nanotubos de carbono en la matriz polimérica. "En esta investigación, hemos dado con la exitosa preparación de uno de estos materiales".
La poli (éter imida) es un polímero que posee muy buenas propiedades mecánicas y térmicas, y se utiliza, entre otras cosas, para hacer piezas interiores de los aviones. Sin embargo, como la gran mayoría de los polímeros, es un material aislante desde el punto de vista eléctrico.
"Añadiendo los nanotubos de carbono, conseguimos no solamente mejorar aún más las propiedades mecánicas de dicho material, sino que además lo hacemos conductor de la electricidad" explica Eguiazabal. Ello puede permitir, entre otras cosas, su utilización en aplicaciones de pintado electrostático.
Desde los inicios, la actividad del Grupo Tecnología de Polímeros integrado en el Departamento de Ciencia y Tecnología de Polímeros y en el Instituto de Materiales Poliméricos, Polymat, de la UPV/EHU, se centró fundamentalmente en el estudio de mezclas de polímeros. La línea de trabajo más reciente del Grupo se centra en el estudio de sistemas nanocompuestos constituidos por polímeros termoplásticos y arcillas laminares modificadas orgánicamente o nanotubos de carbono.
Los nanotubos de carbono tienen unas propiedades mecánicas excelentes, son muy resistentes, muy rígidos, y además, son conductores de la electricidad. "El problema que tienen es que se dispersan, es decir, se mezclan con mucha dificultad con los polímeros" señala Iñaki Eguiazabal, miembro del Grupo de Tecnología de Polímeros, en la nota de prensa de la UPV.
Por ello, es fundamental encontrar métodos que permitan alcanzar un alto grado de dispersión y de estabilidad de los nanotubos de carbono en la matriz polimérica. "En esta investigación, hemos dado con la exitosa preparación de uno de estos materiales".
La poli (éter imida) es un polímero que posee muy buenas propiedades mecánicas y térmicas, y se utiliza, entre otras cosas, para hacer piezas interiores de los aviones. Sin embargo, como la gran mayoría de los polímeros, es un material aislante desde el punto de vista eléctrico.
"Añadiendo los nanotubos de carbono, conseguimos no solamente mejorar aún más las propiedades mecánicas de dicho material, sino que además lo hacemos conductor de la electricidad" explica Eguiazabal. Ello puede permitir, entre otras cosas, su utilización en aplicaciones de pintado electrostático.
Desde los inicios, la actividad del Grupo Tecnología de Polímeros integrado en el Departamento de Ciencia y Tecnología de Polímeros y en el Instituto de Materiales Poliméricos, Polymat, de la UPV/EHU, se centró fundamentalmente en el estudio de mezclas de polímeros. La línea de trabajo más reciente del Grupo se centra en el estudio de sistemas nanocompuestos constituidos por polímeros termoplásticos y arcillas laminares modificadas orgánicamente o nanotubos de carbono.
Mejor dispersión y aumento de la conductividad
Para el caso de la poli (éter imida), han recurrido a incorporar a dicho polímero una mezcla basada en el poli butilén tereftalato (PBT) con una alta concentración de nanotubos dispersos.
En realidad, "el PBT no posee las magníficas propiedades que posee el polímero que estamos intentando mejorar, pero ambos polímeros se mezclan muy bien y de este modo se consigue que dicha dispersión se extienda a toda la mezcla", comenta Eguiazabal, profesor de la Facultad de Ciencias Químicas, al igual que el otro autor del artículo, Imanol González.
"Aunque se produce una reducción de la estabilidad térmica, se consigue conductividad eléctrica con la adición de un 1% de nanotubos de carbono", añade. Por otro lado, "las propiedades mecánicas de la poli éter imida mejoran aún más".
Por último, a todo ello se une el hecho de que la viscosidad de los nanocompuestos se ve notablemente reducida gracias a la presencia del poli butilén tereftalato, lo que supone una mejora apreciable de la procesabilidad de los materiales a pesar de la presencia de los nanotubos que tienden a aumentar la viscosidad. Dicha reducción de la viscosidad permite la obtención de productos con secciones de pequeño espesor o de geometría compleja.
Para el caso de la poli (éter imida), han recurrido a incorporar a dicho polímero una mezcla basada en el poli butilén tereftalato (PBT) con una alta concentración de nanotubos dispersos.
En realidad, "el PBT no posee las magníficas propiedades que posee el polímero que estamos intentando mejorar, pero ambos polímeros se mezclan muy bien y de este modo se consigue que dicha dispersión se extienda a toda la mezcla", comenta Eguiazabal, profesor de la Facultad de Ciencias Químicas, al igual que el otro autor del artículo, Imanol González.
"Aunque se produce una reducción de la estabilidad térmica, se consigue conductividad eléctrica con la adición de un 1% de nanotubos de carbono", añade. Por otro lado, "las propiedades mecánicas de la poli éter imida mejoran aún más".
Por último, a todo ello se une el hecho de que la viscosidad de los nanocompuestos se ve notablemente reducida gracias a la presencia del poli butilén tereftalato, lo que supone una mejora apreciable de la procesabilidad de los materiales a pesar de la presencia de los nanotubos que tienden a aumentar la viscosidad. Dicha reducción de la viscosidad permite la obtención de productos con secciones de pequeño espesor o de geometría compleja.
Referencia bibliográfica:
I. González, J.I. Eguiazabal. Widely dispersed PEI-based nanocomposites with multi-wall carbon nanotubes by blending with a masterbatch. Composites Part A: Applied Science and Manufacturing, (2013). DOI: 10.1016/j.compositesa.2013.06.011.
I. González, J.I. Eguiazabal. Widely dispersed PEI-based nanocomposites with multi-wall carbon nanotubes by blending with a masterbatch. Composites Part A: Applied Science and Manufacturing, (2013). DOI: 10.1016/j.compositesa.2013.06.011.